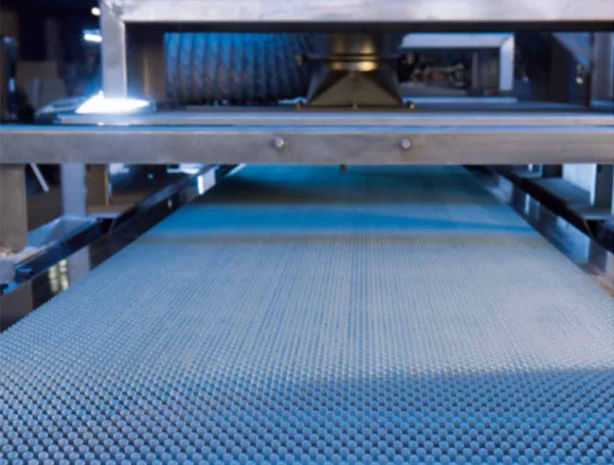
In the material processing industry, efficient and precise granulation methods are critical for ensuring high product quality and operational profitability. Among the diverse range of granulation technologies, the steel belt granulator has emerged as a game-changer, offering unparalleled advantages in handling heat-sensitive, viscous, and low-melting-point materials. This article Little Sky delves into the key features and best practices for operating a steel belt granulator, highlighting why it is an indispensable tool in modern industrial processes.
Key Features of a Steel Belt Granulator
1. High-Quality Steel Belt
The steel belt is the central component of a steel belt granulator, designed for strength and durability under extreme operating conditions. Typically made from premium-grade stainless steel or carbon steel, these belts are engineered to resist corrosion, high temperatures, and wear over long periods of use. Their smooth, flat surfaces prevent molten material from sticking during the cooling process, ensuring efficient operation and consistent quality. Additionally, the belt's uniform surface aids in precise granule formation, enabling manufacturers to meet stringent quality standards across diverse industrial applications.
2. Advanced Cooling Mechanisms
Cooling plays a critical role in the granulation process, ensuring the rapid and uniform solidification of molten materials. Steel belt granulators feature advanced cooling systems, employing water, air, or a combination of both to quickly reduce the temperature of materials as they travel along the belt. These systems are meticulously designed to distribute cooling evenly across the entire surface, preventing thermal stress and ensuring the production of high-quality granules. Furthermore, the efficient cooling mechanism enhances process reliability and minimizes material defects, contributing to higher production yields.
3. Flexible Granule Size Adjustment
One of the most versatile features of steel belt granulators is their ability to produce granules in a wide range of sizes. This flexibility is achieved through adjustable parameters such as material feed rate, cooling duration, and the configuration of cutting mechanisms. By fine-tuning these variables, manufacturers can customize the granulation process to produce anything from ultra-fine powders for specialized industries like pharmaceuticals to larger, more robust granules used in construction or chemical manufacturing. This adaptability makes steel belt granulators a valuable asset for industries requiring tailored production capabilities.
4. Continuous Operation
The continuous operation of steel belt granulators is a key advantage for high-capacity manufacturing environments. The constant movement of the steel belt facilitates seamless material handling, allowing for uninterrupted production cycles. This capability ensures consistent output and minimizes downtime, making it particularly beneficial for industries with high-volume production demands, such as petrochemicals, plastics, and food processing. Additionally, the continuous process reduces operational complexities and enhances overall process efficiency, providing manufacturers with a competitive edge.
5. Low Maintenance Requirements
Steel belt granulators are engineered for longevity and reliability, minimizing maintenance demands and associated costs. The robust construction of the steel belt resists wear and tear even under heavy use, while its self-cleaning properties prevent material buildup and reduce cleaning time. This results in prolonged equipment life, fewer maintenance interruptions, and significant cost savings over time. Furthermore, the straightforward design and user-friendly operation simplify routine inspections and upkeep, ensuring that manufacturers can maintain high productivity with minimal effort. This combination of durability and efficiency makes steel belt granulators a cost-effective choice for a wide range of industrial applications.
Best Practices for Operating a Steel Belt Granulator
To achieve optimal performance and longevity from a steel belt granulator, consider the following best practices:
1. Regular Maintenance
Maintaining a steel belt granulator involves more than occasional checks; it requires a structured maintenance schedule to identify and address potential issues before they escalate. Inspect critical components such as the steel belt, cooling mechanisms, cutting tools, and conveyor drive systems regularly. Look for signs of wear, misalignment, or damage. Lubricate moving parts and ensure the tension of the steel belt is within recommended specifications. Periodically recalibrate sensors and controls to maintain operational accuracy. Proactive maintenance extends the lifespan of the granulator and reduces costly unplanned downtimes, ensuring smooth and uninterrupted production cycles.
2. Material Compatibility
Understanding the materials being processed is critical to avoiding operational inefficiencies and equipment damage. The steel belt and cooling systems are designed to handle specific material properties, such as melting point, viscosity, and corrosiveness. Processing materials outside the equipment's design specifications can lead to overheating, chemical reactions, or excessive residue buildup. For example, highly viscous or corrosive materials may require specialized coatings on the steel belt or alternative cooling system configurations. Regularly consult material data sheets and ensure the steel belt granulator is appropriately configured for the materials being processed to optimize performance and minimize wear.
3. Precise Temperature Control
Granule formation and quality depend heavily on maintaining precise and uniform cooling temperatures throughout the granulation process. Sudden temperature fluctuations can lead to uneven solidification, weak granules, or surface defects. Utilize advanced cooling control systems of steel belt granulators that monitor temperature across the entire belt surface and adjust cooling rates in real time. Additionally, ensure that cooling fluids (e.g., water or air) are clean and free of contaminants to prevent clogging or inefficiency. Consistent temperature control not only improves product quality but also enhances the efficiency of the overall process.
4. Proper Cleaning
Residue buildup on the steel belt or feeding system can cause several problems, including uneven material flow, reduced cooling efficiency, and contamination of the final product. Establish a routine cleaning protocol to remove residue, especially when switching between different materials. Use non-abrasive cleaning tools or chemicals compatible with the steel belt material to prevent surface damage. For systems equipped with self-cleaning mechanisms, ensure they are operating correctly and inspect them periodically for wear. A clean steel belt granulator not only ensures product quality but also reduces the risk of long-term operational issues.
5. Operator Training
The human element is often the most critical factor in achieving optimal steel belt granulator performance. Ensure that all operators receive comprehensive training covering equipment operation, routine maintenance, safety procedures, and troubleshooting techniques. Well-trained operators can identify early warning signs of equipment failure, make precise adjustments to settings, and respond promptly to production anomalies. Regular training refreshers and updates on new technologies or procedures ensure that the team remains skilled and capable of maximizing the granulator's potential.
The steel belt granulator has revolutionized granulation technology, offering unmatched efficiency, precision, and versatility. Its ability to handle a diverse range of materials and deliver consistent, high-quality granules makes it an essential tool in industries such as chemicals, polymers, food, and pharmaceuticals. With proper operation and maintenance, this equipment ensures high throughput, reduced operational costs, and superior product quality, making it an indispensable asset for modern manufacturing.
https://www.th-littlesky.com/PRODUCT
www.th-littlesky.com
Little Sky Mechanical Engineering Kabushiki Kaisha