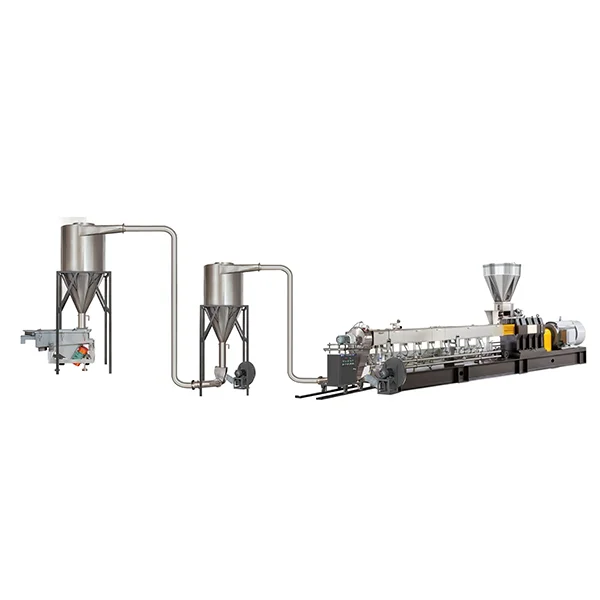
In the plastic processing industry, achieving high efficiency and superior product quality requires more than just a reliable extruder. Extruder auxiliary parts play a crucial role in optimizing performance, reducing downtime, and ensuring smooth operations. Whether you're working with twin-screw extruders, single-screw extruders, sheet production lines, or PET recycling lines, the right auxiliary components can significantly enhance productivity.
As a leading manufacturer in the plastic industry, JiaXin Mechanical Manufacture specializes in designing and manufacturing extruders and molding machinery, offering turnkey solutions for compounding, recycling, and sheet production lines. With expertise in twin-screw extruders, single-screw extruders, and PET recycling systems, JiaXin provides top-quality extruder auxiliary parts that improve efficiency and prolong the lifespan of your equipment.
In this article, we’ll explore essential extruder auxiliary parts and how they contribute to better performance and higher productivity in plastic processing.
1. Feeding Systems: Ensuring Precise Material Input
A reliable feeding system is critical for maintaining consistent material flow in an extruder. Auxiliary feeding components include:
-
Volumetric and Gravimetric Feeders – Control the precise amount of material entering the extruder, reducing waste and improving formulation accuracy.
-
Hopper Dryers and Dehumidifiers – Essential for materials like PET, as they remove moisture before extrusion to prevent defects like bubbles and inconsistencies.
-
Side Feeders – Used in twin-screw extruders for adding additives or fillers during the process.
How JiaXin Helps: JiaXin provides advanced feeding and drying solutions tailored for compounding and recycling production lines, ensuring consistent performance.
2. Melt Pumps: Stabilizing Flow and Pressure
Melt pumps are essential for maintaining uniform pressure and flow in extrusion, reducing strain on the extruder screw and ensuring consistent output. These pumps:
-
Enhance material homogeneity
-
Improve dimensional accuracy in the final product
-
Reduce energy consumption by optimizing extruder workload
How JiaXin Helps: JiaXin integrates high-precision melt pump systems with its sheet production and recycling lines, optimizing material processing efficiency.
3. Screen Changers and Filters: Protecting Extruders from Contaminants
Screen changers and filters remove impurities from molten plastic before it reaches the die, preventing defects and extending machine life. Key types include:
-
Manual and Hydraulic Screen Changers – Allow quick screen replacement without stopping production.
-
Continuous Filtration Systems – Used in recycling lines, ensuring non-stop production while filtering contaminants.
How JiaXin Helps: JiaXin’s PET recycling production lines are equipped with high-efficiency filtration systems, ensuring clean, high-quality material output.
4. Cooling and Calibration Systems: Controlling Product Quality
After extrusion, the plastic must be cooled and shaped properly. Auxiliary cooling systems include:
-
Water Cooling Tanks – Used in pipe and profile extrusion to rapidly cool extruded material.
-
Air Cooling Systems – Ideal for sheet and film extrusion to prevent warping.
-
Calibration Tables – Ensure uniform thickness and smooth surfaces in sheet production lines.
How JiaXin Helps: JiaXin’s customized cooling and calibration solutions help manufacturers achieve high-precision extrusion results.
5. Cutting and Pelletizing Systems: Finalizing the Product
For compounding and recycling lines, cutting and pelletizing systems transform extruded material into uniform pellets for further processing. These systems include:
-
Hot Die Face Pelletizers – Ideal for high-viscosity polymers.
-
Strand Pelletizers – Commonly used in twin-screw extruder applications.
-
Underwater Pelletizing Systems – Used for high-output production lines requiring uniform granules.
How JiaXin Helps: JiaXin integrates cutting-edge pelletizing technology into its compounding and recycling extruders, ensuring consistent pellet quality.
6. Die Heads and Molds: Shaping the Final Product
The die head is one of the most crucial auxiliary components in extrusion, determining the final shape and dimensions of the product. Various die types include:
-
Flat Dies – Used for sheet extrusion to achieve even thickness.
-
Profile Dies – Used for making customized plastic profiles.
-
Underwater Die Heads – Utilized in high-output recycling lines.
How JiaXin Helps: JiaXin manufactures precision-engineered die heads tailored for different applications, ensuring superior product quality.
7. Conveyor and Take-Off Systems: Streamlining Production Flow
Once the extruded product is cooled and shaped, conveyors and take-off units transport it to the next processing stage. Key systems include:
-
Belt Conveyors – Move extruded materials smoothly.
-
Haul-Off Units – Used in pipe and profile extrusion to ensure even pulling speed.
-
Stacking and Winding Machines – Essential in sheet and film production for automated handling.
How JiaXin Helps: JiaXin’s high-efficiency take-off and stacking solutions improve production line automation, reducing labor costs.
Conclusion
Extruder auxiliary parts are vital for optimizing efficiency, product quality, and equipment longevity in plastic processing. Whether you’re working with compounding, recycling, or sheet production lines, the right auxiliary components help reduce downtime, improve material flow, and enhance overall performance.
As a professional manufacturer specializing in extruders and turnkey production solutions, JiaXin Mechanical Manufacture provides high-quality auxiliary parts that integrate seamlessly with twin-screw extruders, single-screw extruders, PET recycling lines, and sheet production systems.
For customized extrusion solutions that improve efficiency and product quality, partner with JiaXin Mechanical Manufacture today!
www.tcextruder.com
JiaXin Mechanical Manufacture CO., Ltd