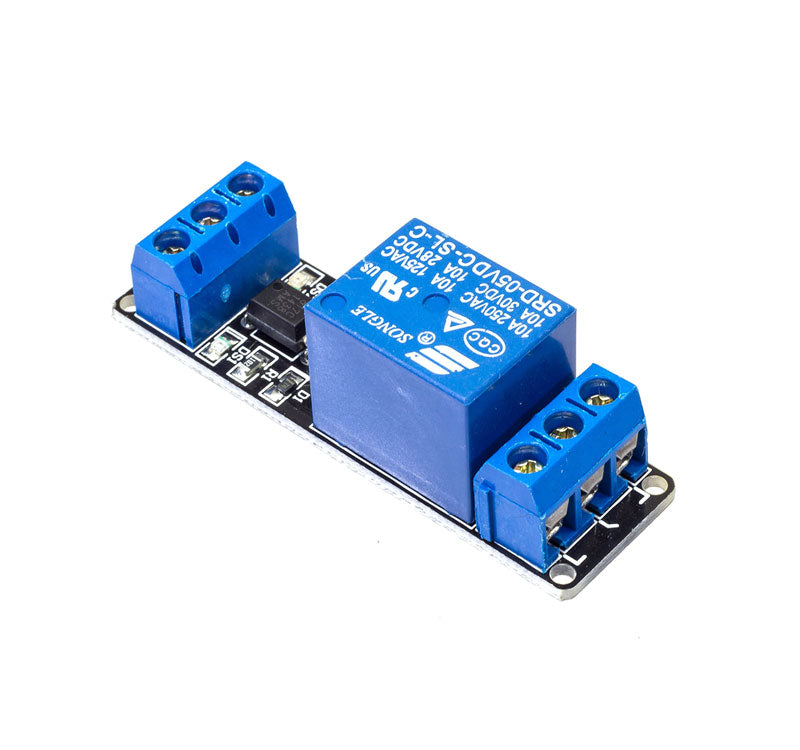
In the realm of power control, two prominent technologies have emerged as frontrunners: Silicon Controlled Rectifier (SCR) and Solid State Relay (SSR). Both SCR and SSR play crucial roles in various industries, but determining which one is better requires a comprehensive analysis. This article aims to delve into the intricacies of SCR and SSR, comparing their features, advantages, and applications, ultimately shedding light on the superior choice for power control.
- Understanding SCR:
Silicon Controlled Rectifier (SCR), also known as thyristor, is a semiconductor device widely used for power control applications. SCR operates as a switch, allowing current flow in one direction when triggered by a control signal. Its key features include high voltage and current handling capabilities, low cost, and robustness. SCR finds extensive usage in industries such as motor control, heating systems, and high-power lighting. - Exploring SSR:
Solid State Relay (SSR) is an electronic switching device that utilizes semiconductor components to control power flow. Unlike SCR, SSR does not rely on mechanical parts, making it more reliable and durable. SSR offers advantages such as fast switching speed, high precision, noiseless operation, and optical isolation. These features make SSR suitable for applications requiring precise control, such as temperature control systems, industrial automation, and medical equipment. - Performance Comparison:
a. Power Handling Capacity:
SCRs excel in handling high voltage and current levels, making them ideal for heavy-duty applications. They can handle currents ranging from a few amperes to several kiloamperes, making them suitable for industrial machinery and power distribution systems. On the other hand, SSRs have lower power handling capabilities, typically ranging from a few milliamperes to tens of amperes. SSRs are more suitable for low to medium power applications, where precise control and fast switching speed are crucial.
b. Reliability and Durability:
SCRs are known for their robustness and ability to withstand harsh environments. They can handle high surge currents and have a longer lifespan compared to SSRs. However, SSRs have no mechanical parts, eliminating the risk of wear and tear. This makes SSRs more reliable in applications where frequent switching is required, as they have no physical contacts to degrade over time.
c. Control and Precision:
SSRs offer superior control and precision due to their fast switching speed and ability to provide precise current regulation. They can switch on and off rapidly, allowing for accurate control of power output. Additionally, SSRs provide isolation between the control and power circuits, minimizing the risk of electrical interference. SCR control, although effective, may not offer the same level of precision and isolation as SSRs.
- Application Scenarios:
a. SCR Applications:
- Motor control in heavy machinery and electric vehicles.
- High-power lighting systems, such as stadium floodlights.
- Heating systems, including industrial furnaces and electric ovens.
- Power distribution systems and rectifiers.
b. SSR Applications:
- Temperature control systems in HVAC (Heating, Ventilation, and Air Conditioning).
- Industrial automation and robotics.
- Medical equipment, such as MRI machines and laser systems.
- Photovoltaic (PV) systems for solar energy generation.
Conclusion:
In conclusion, both SCR and SSR have their unique strengths and applications. SCR excels in high-power, heavy-duty scenarios, offering robustness and high voltage/current handling capabilities. On the other hand, SSR provides precise control, fast switching speed, and reliability in low to medium power applications. When choosing between SCR and SSR, it is essential to consider the specific requirements of the application, such as power levels, control precision, and environmental conditions. By understanding the nuances of these technologies, one can make an informed decision to ensure optimal power control in various industries.